اجزای سازنده قالب تزریق پلاستیک:
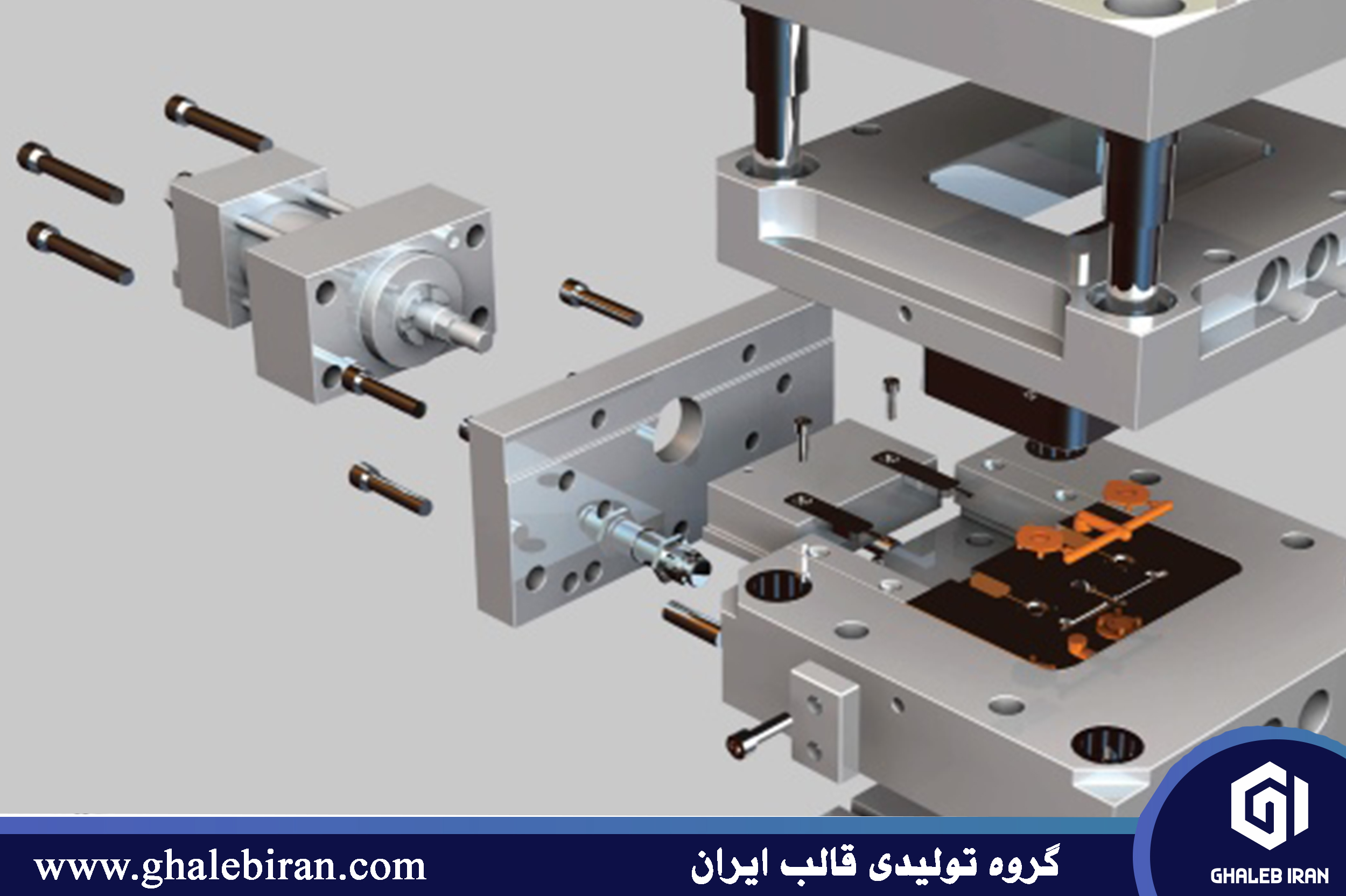
روند کار در یک دستگاه تزریق پلاستیک که در فاصله زمانی تقریبا 2 ثانیه تا 2 دقیقه انجام میگیرد عبارت است از: ذوب شدن رزین، فرایند تزریق آن به سیستم، قالب گیری و درانتهای کار نیز خارج نمودن قطعه از درون قالب می باشد. اغلب قالب تزریق پلاستیک از دو بخش اصلی به نام های حفره (cavity) و همچنین بخش هسته (core) شکل گرفته است که محصول نهایی به کمک قرار گرفتن پلاستیک مذاب میان این دو بخش و سپس خنک نمودن این مواد تولید میگردد.
درواقع به هنگام بسته شدن قالب با اعمال فشار زیاد رزین ذوب شده در حد فاصل بخش حفره و بخش هسته تزریق می گردد. جالب است بدانید که در اصطلاح عامیانه به بخش حفره، کویته و به بخش هسته، ماهیچه نیز گفته میشود. همچنین چگونگی مدل و نوع شکل سفارش قطعه درواقع تعیین کننده میزان کویته های موجود در قالب تزریق پلاستیک می باشد.
با این تفاسیر قالب تزریق خود متشکل از دو سیستم می باشد. یکی سیستمی که در بخش عقب کویته قرار میگیرد و به نام سیستم تزریق شناخته میگردد و سیستم دیگر در قسمت ماهیچه قرار گرفته می شود وسیستم پران نامیده می شود. هریک از این سیستم های قالب تزریق خود از اجزای مختلفی به شرح زیر تشکیل شده است:
-
کانال تزریق مذاب (اجزای سازنده قالب تزریق پلاستیک)
یکی از بخش های مهم و اساسی که قبل از مرحله قالب گیری صورت میگیرد قسمت تزریق پلاستیک می باشد. این قسمت شامل دو صفحه ی مخصوص قالب گیری بوده که از بخش نازل ماشین شروع و به بخش کانال های انتهایی ختم می گردد. اسپرو نامی است که به کانال اولیه جهت ورود مواد ذوب شده اطلاق می گردد.
جهت راهنمایی صحیح مواد ذوب شده به درون قالب از حلقه جاگیری یا به عبارتی حلقه تنظیم و بوش اسپرو استفاده میگردد از آنجا که همواره قالب ها در معرض فشار بالای سیلندر میباشند تنظیم نمودن مطلوب تمامی این حلقه ها جهت عدم حرکت درآمدن قالب به دلیل اعمال این فشار از اهمیت بالایی برخوردار می باشد. نکته دیگر اینکه چون قطعه بوش اسپرو در دمای بالا در معرض فشار و همچنین سایش قرار میگیرد بهتراست که جهت تولید آن از آلیاژهای مقاوم و همچنین انواع مختلفی از پوشش ضد سایش استفاده نمود.
جالب است که بدانید بعد از قرارگیری مواد مذاب در قسمت کویته قالب، سیستم سرمایشی تعبیه شده در قالب از طریق راهگاهی شروع به کار نموده و به این ترتیب فرایند خنک شدن سطح تماس قالب با مواد مذاب آغاز می گردد. درواقع دمای پایین این راهگاه ها به کمک عبور همواره و دائمی مایعات خنک از درون آن شکل میگیرد.
همچنین سرعت دستگاه، میزان قدرت سرمایشی راهگاه های خنک کننده را تعیین می نماید به طوریکه تا وقتی قطعه کاملا خنک نشده است قالب نیز باز نمی گردد. میزان زمان مورد نیازجهت خنک شدن قطعه نهایی تحت تاثیر دو عامل خواص ترمودینامیکی پلاستیک و بیشترین ضخامت موجود در دیواره ی آن قرار دارد.
-
کانالهای گرمایشی (اجزای سازنده قالب تزریق پلاستیک)
ازجمله مشکلات پیش رو در طول مسیر تولید، جهت عبور مواد ذوب شده از بخش نازل تا بخش کویته درواقع سرد شدن زود هنگام مواد مذاب در طی مسیر می باشد که نهایتا سبب ایجاد نتیجه نامطلوب در قالب گیری می گردد که این مشکل با قرارگیری کانال های گرمایشی در بخش اسپرو و همچنین مسیر عبور مواد ذوب شده برطرف می گردد.
در میان دو صفحه قالب گیری، دریچه هایی جهت هواگیری قرار گرفته می شوند. اما اصلا هوا چگونه وارد قالب می گردد؟ درواقع در زمان بستن قالب ها ممکن است میزانی از هوا نیز بین دو صفحه کویته و ماهیچه محبوس گردد اما آنچه که باید بدان توجه داشت این است که در صورت باقی ماندن هوا در بین صفحات ممکن است با پدیده هایی ازجمله بالا رفتن دور از انتظار دما و همچنین سوخت مواد مذاب روبرو گردیم که تمامی اینها درنهایت سبب تولید و ساخت محصولات بدون کیفیت خواهد شد.
-
سیستم پران (اجزای سازنده قالب تزریق پلاستیک)
همانطور که میدانیم بعد از مراحل تزریق و قالب گیری و همچنین بعد از مرحله سرد شدن به دلیل چسبیدن قطعه به درون قالب، نوبت به جدا شدن قطعه از قالب تزریق پلاستیک می گردد. پران درواقع مکانیزمی است که با کمک آن بدون کوچکترین آسیب به قطعه کار جداسازی انجام می گیرد. سیستم پران دارای اجزای متفاوتی ازجمله: میله، جعبه، صفحههای پران و همچنین چند پین پران در قسمت پشتی ماهیچه قالب می باشد.
روش کار در سیستم پران بدین صورت بوده که با باز شدن گیره دستگاه، شاهد جابجایی در میله پران شده که درنهایت همه اینها خود سبب فعال شدن سیستم پران می گردد. با فعال شدن سیستم پران نیز، صفحه پران به عقب رفته وسپس قطعه به وسیله پین های پران از قالب جدا شده و به خارج پرتاب می گردد.
همچنین جهت خروج آسان و راحت قطعه از درون قالب اغلب بر روی بخش ماهیچه شروع به اسپری نمودن عوامل جداکننده مین مایند.(همانطور که گفتیم وظیفه این مواد جدا کننده، جدا شدن سریع قطعه از درون قالب می باشد.)